ریخته گری پیوسته در تولید میلگرد
ریختهگری پیوسته (به انگلیسی Continuous Casting) یک فناوری پیشرفته مورد استفاده در صنعت فولاد و کارخانجات فولادسازی است که برای تولید انواع مقاطع فولادی مانند میلگرد، شمش، ورق و پروفیلهای مختلف بهکار میرود. این فرآیند از اهمیت ویژهای در تولید میلگرد دارد و نتایج مثبت زیادی در کیفیت، بهرهوری و کاهش هزینهها به همراه دارد. شما […]
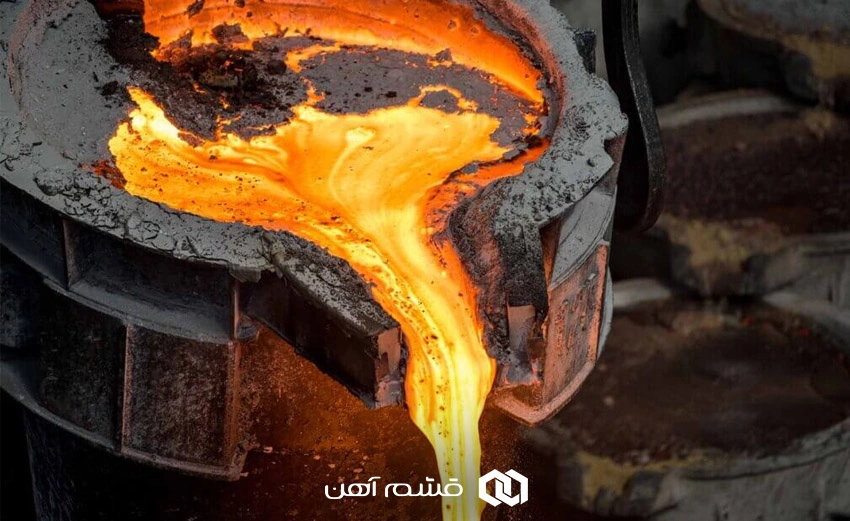
ریختهگری پیوسته (به انگلیسی Continuous Casting) یک فناوری پیشرفته مورد استفاده در صنعت فولاد و کارخانجات فولادسازی است که برای تولید انواع مقاطع فولادی مانند میلگرد، شمش، ورق و پروفیلهای مختلف بهکار میرود. این فرآیند از اهمیت ویژهای در تولید میلگرد دارد و نتایج مثبت زیادی در کیفیت، بهرهوری و کاهش هزینهها به همراه دارد. شما کاربران محترم سایت قشم آهن میتوانید در صورت تمایل «همکاری گل گهر و جهان فولاد سیرجان» را مطالعه بفرمایید. درادامه مقاله ریخته گری پیوسته در تولید میلگرد وبلاگ قشم آهن تامین کننده میلگرد جهان فولاد سیرجان، فرآیند ریختهگری پیوسته و مزایای آن در تولید میلگرد شرح داده شده است؛ با ما همراه باشید.
در این مقاله میخوانید
ریخته گری پیوسته در تولید میلگرد
ریختهگری پیوسته فرآیندی است که در آن فولاد مذاب به صورت پیوسته از کوره قوس الکتریکی یا کورههای دیگر به قالبهای ریختهگری منتقل میشود. در این روش، فولاد مذاب به جای ریختهگری در قالبهای ثابت (که در آن نیاز به قطع و شروع مجدد فرآیند وجود دارد)، به صورت پیوسته از یک کوره به قالبهایی با شکل مقطع موردنظر (مانند میلگرد) منتقل میشود و به نوعی ریخته گری پیوسته در تولید میلگرد تکمیل میشود.
تاریخچه ریخته گری پیوسته
روش ریخته گری پیوسته ابتدا در دهههای 1960 به عنوان یک نوآوری در صنعت فولاد معرفی شد و در طول زمان، به یکی از رایجترین روشها برای تولید مقاطع فولادی تبدیل شد. به طور کلی اولین سیستمهای ریختهگری پیوسته در اوایل دهه 1970 میلادی به مرحله تجاری رسیدند. این سیستمها بهویژه در کارخانههای بزرگ فولادسازی بهکار گرفته شدند و به سرعت جایگزین روشهای سنتی ریختهگری شدند و ریختهگری پیوسته برای تولید انواع مقاطع فولادی، از جمله شمش، ورق و میلگرد، به کار گرفته شد و این تغییرات باعث شد که فرآیند تولید فولاد بسیار کارآمدتر شود.
در دهه 1980 میلادی، استفاده از ریختهگری پیوسته به طور گستردهای در صنعت فولاد جهانی گسترش یافت. این فناوری به سرعت در کشورهای صنعتی پیشرفته و همچنین در کشورهای در حال توسعه بهویژه در آسیا و آمریکای لاتین بهکار گرفته شد. امروزه ریختهگری پیوسته به یکی از فناوریهای استاندارد در صنعت فولاد تبدیل شده است و بسیاری از کارخانههای فولاد از این فناوری برای تولید میلگرد، شمش، ورق و دیگر محصولات فولادی استفاده میکنند. ریختهگری پیوسته نه تنها به کاهش ضایعات و هزینهها کمک کرده، بلکه تولید محصولات فولادی با کیفیت و متنوع را به یک امر ممکن و کارآمد تبدیل کرده است.
فرآیند ریختهگری پیوسته در تولید میلگرد
8 مرحله مهم در ریخته گری پیوسته در تولید میلگرد عبارت اند از:
- ذوب و آمادهسازی فولاد مذاب
- انتقال فولاد مذاب
- انجماد اولیه در قالب
- خروج از قالب و انتقال به نورد
- کنترل دمای فولاد در نورد
- برش به طولهای مشخص
- خنکسازی نهایی
- بازرسی و کنترل کیفیت
8 مرحله ریخته گری پیوسته در تولید میلگرد
در فرآیند ریختهگری پیوسته میلگرد، مراحل زیر طی میشود:
ذوب و آمادهسازی فولاد مذاب
در ابتدای فرآیند ریختهگری پیوسته، فولاد مورد نیاز باید در یک کوره ذوب شود. این کورهها معمولاً کورههای قوس الکتریکی یا کورههای القایی هستند که با استفاده از برق یا امواج الکترومغناطیسی، فولاد را تا دمای لازم برای ذوب (حدود 1500 درجه سانتیگراد) گرم میکنند.
آمادهسازی ترکیب شیمیایی: ترکیب شیمیایی فولاد در این مرحله با افزودن آلیاژهای مختلف (مانند کربن، منگنز، سیلیسیم، کروم و…) برای ایجاد خواص مطلوب انجام میشود.
پاتیل یا تشتک تغذیه: فولاد مذاب از کوره ذوب به یک پاتیل یا تشتک تغذیه منتقل میشود، که این تشتک نقش مخزن برای نگهداری و انتقال فولاد مذاب به فرآیندهای بعدی را دارد.
انتقال فولاد مذاب
در این مرحله، فولاد مذاب از پاتیل یا تشتک تغذیه به قسمت اصلی فرآیند ریختهگری پیوسته منتقل میشود. این فولاد مذاب به شکل مداوم وارد قالبهای ریختهگری پیوسته میشود. قالبهای ریختهگری معمولاً از مس یا آلیاژهای مس ساخته میشوند که به دلیل رسانایی بالا، قادر به جذب و انتقال حرارت زیاد هستند. این قالبها باید قادر باشند فولاد مذاب را به شکلی منسجم و یکنواخت درآورند.
انجماد اولیه در قالب
در قالب ریختهگری پیوسته، فولاد مذاب به سرعت شروع به سرد شدن میکند. این فرآیند انجماد در قالب صورت میگیرد و فولاد مذاب به بلوک نیمهجامد تبدیل میشود. برای کنترل دقیق دمای فولاد در این مرحله، از سیستمهای خنککننده که معمولاً به صورت جریان آب یا هوا در اطراف قالبها قرار دارند، استفاده میشود. این سیستمها نقش حیاتی در جلوگیری از انجماد سریع یا ناگهانی فولاد دارند که میتواند منجر به ترکهای سطحی یا مشکلات دیگر در ساختار فولاد شود.
خروج از قالب و انتقال به نورد
پس از اینکه فولاد در قالب به اندازه کافی سرد شد و به یک بلوک نیمهجامد تبدیل شد، از قالب خارج شده و وارد مرحله بعدی فرآیند میشود. این مرحله شامل عبور فولاد از نورد و تبدیل آن به مقاطع مختلف است.
بلوکها یا شمشهای نیمهجامد از قالبها به دستگاههای نورد پیوسته منتقل میشوند. در این مرحله، بلوکها با اعمال فشار و دما در غلتکهای نورد قرار گرفته و به میلگردهایی با قطر یا مقطع مورد نظر تبدیل میشوند. این فرآیند بهطور مداوم ادامه دارد و باعث تغییر شکل مقطع و کاهش ضخامت میشود.
کنترل دمای فولاد در نورد
در این مرحله، فولاد باید در دمایی معین باقی بماند تا کیفیت سطح و خواص مکانیکی مطلوبی حاصل شود. در همین راستا، از سیستمهای خنککننده مختلف برای کنترل دمای فولاد استفاده میشود. پس از نورد، فولاد همچنان باید بهطور یکنواخت و تدریجی سرد شود تا از بروز تنشهای داخلی و ترکها جلوگیری شود. این خنکسازی معمولاً به دو صورت انجام میشود: خنکسازی اولیه (با آب یا هوای کنترلشده) و خنکسازی نهایی در داخل تونلهای خاص.
برش به طولهای مشخص
پس از آنکه میلگرد به مقطع و ابعاد مورد نظر رسید، مرحله برش انجام میشود. میلگردها معمولاً به طولهای مختلف بر اساس نیاز مشتری یا استانداردهای صنعتی برش داده میشوند.این برشها میتوانند بهصورت خودکار و با دقت بالا توسط دستگاههای برش انجام شوند.
خنکسازی نهایی
در این مرحله، میلگردها پس از برش به طور کامل و دقیق سرد میشوند. این خنکسازی باید بهگونهای انجام شود که از آسیب دیدن خواص فولاد جلوگیری کرده و مقاطع تولیدی به استحکام و انعطافپذیری مناسب دست یابند.
بازرسی و کنترل کیفیت
در مرحله نهایی، میلگردها باید مورد بازرسیهای دقیق کیفیت قرار گیرند. این کنترل شامل بررسی ابعاد، سطح، استحکام، و سایر ویژگیهای مکانیکی است.
- آزمونهای مختلف: آزمونهای غیرمخرب مانند آزمایشهای سختی، تستهای کششی و آزمایشهای بصری برای اطمینان از عدم وجود نقص در میلگردها انجام میشود.
- گواهی کیفیت: پس از تأیید کیفیت، میلگردهای تولید شده آماده ارسال به بازار یا کارخانههای ساخت و ساز میشوند.
مزایا ریخته گری پیوسته میلگرد
در این قسمت از مقاله ریخته گری پیوسته در تولید میلگرد مزایا این روش شرح داده شده است؛ با ما همراه باشید.
5 مزیت ریخته گری پیوسته میلگرد
- کیفیت بالا و یکنواخت میلگرد
- سرعت بالا
- کاهش هزینه تولید میلگرد
- کنترل بهتر خواص مکانیکی
- دقت ابعادی و یکنواختی بهتر
در ادامه هریک از مزایا ریخته گری پیوسته شرح داده شده است:
کیفیت بالا و یکنواخت میلگرد
در ریختهگری پیوسته، فرآیند تولید میلگرد به صورت پیوسته و بدون وقفه انجام میشود که باعث کاهش خطر عیوبی چون ترکخوردگی، حفرههای گازی و ناخالصیهای فلزی در مقاطع نهایی میشود. همچنین با کاهش فرآیندهای اضافی، از جمله تصفیههای مجدد، کیفیت سطحی محصول بهبود یافته و احتمال وجود نقصهای سطحی کاهش مییابد.
سرعت بالا
ریختهگری پیوسته امکان تولید پیوسته و مداوم میلگردها را فراهم میآورد، که به کاهش زمانهای توقف و آمادهسازی میانجامد. این فرآیند به دلیل عدم نیاز به ذوب مجدد و نگهداری مواد، باعث افزایش کارایی و بهرهوری میشود.
کاهش هزینه تولید میلگرد
به دلیل سادهتر بودن فرآیند و کاهش مراحل تولید، هزینههای مربوط به تجهیزات، نیروی انسانی و مواد اولیه کاهش مییابد. همچنین، به دلیل تولید پیوسته و بهینه، ضایعات نیز کاهش پیدا میکند.
کنترل بهتر خواص مکانیکی
در این فرآیند، ساختار دانهای فولاد بهتر کنترل میشود که به نتایج مطلوبتری در خصوص خواص مکانیکی مانند مقاومت کششی، سختی و دوام میلگردها منجر میشود. همچنین به دلیل یکنواختی بیشتر ساختار، احتمال بروز مشکلاتی چون ضعف در نواحی خاص محصول کاهش مییابد.
دقت ابعادی و یکنواختی بهتر
فرآیند ریختهگری پیوسته امکان کنترل دقیق ابعاد و یکنواختی ضخامت محصولات را فراهم میآورد. همچنین این ویژگی باعث میشود که میلگردها به طور دقیقتری طبق استانداردهای مورد نیاز تولید شوند.
پایان | وبلاگ قشم آهن (فولاد ابرکاوان قشم)
استعلام قیمت میلگرد جهان فولاد سیرجان
کاربران محترم سایت قشم آهن لطفاً توجه داشته باشید جهت استعلام قیمت روز انواع سایزهای میلگرد جهان فولاد سیرجان درب کارخانه به همراه اطلاع از تخفیفات ویژه مشتریان شرکت فولاد ابرکاوان، با شماره 09129596001 تماس حاصل فرمایید و یا با ورود به صفحه قیمت میلگرد، از نرخ روز مطلع شوید. همچنین با قابلیت نمودار قیمت ها میتوانید به راحتی نوسان قیمت مقاطع فولادی را مشاهده کرده و بازار آهن آلات را تحلیل کنید.
دیدگاه کاربران (0 دیدگاه)
اولین دیدگاه را شما ثبت کنید.