فرآیند تولید شمش فولادی
شمش فولادی یکی از مهمترین مواد اولیه برای تولید میلگرد است. در فرآیند تولید میلگرد، شمش فولادی بهعنوان یک محصول میانی استفاده میشود که در ادامه با پردازشهای مختلف به میلگرد تبدیل میشود. به طور مثال کارخانه جهان فولاد سیرجان با تولید شمش فولادی مرغوب، از آن به عنوان مواد اولیه خط تولید میلگرد آجدار […]
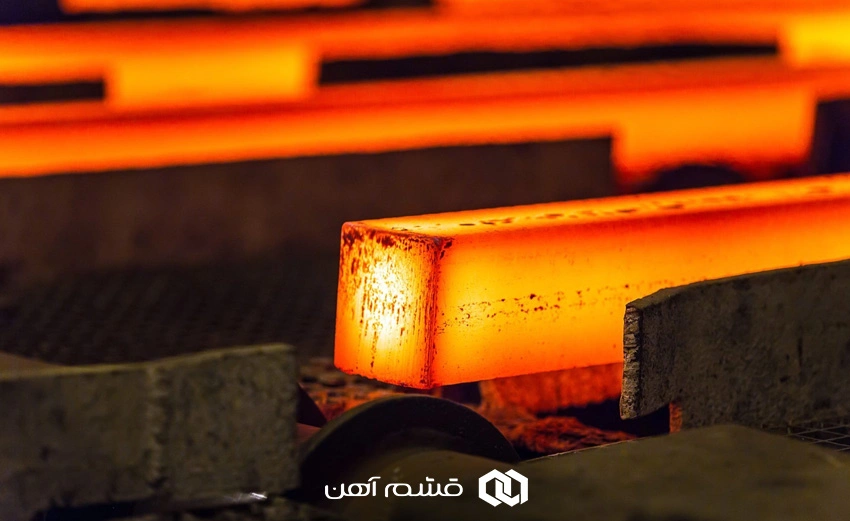
شمش فولادی یکی از مهمترین مواد اولیه برای تولید میلگرد است. در فرآیند تولید میلگرد، شمش فولادی بهعنوان یک محصول میانی استفاده میشود که در ادامه با پردازشهای مختلف به میلگرد تبدیل میشود. به طور مثال کارخانه جهان فولاد سیرجان با تولید شمش فولادی مرغوب، از آن به عنوان مواد اولیه خط تولید میلگرد آجدار استفاده میکند. در ادامه مقاله قشم آهن تامین کننده انوع سایز های میلگرد جهان فولاد سیرجان همراه باشید. همچنین در صورت تمایل میتوانید تاریخچه تولید میلگرد را نیز مطالعه بفرمایید.
در این مقاله میخوانید
فرآیند تولید شمش فولادی
فرآیند تولید شمش فولادی، از استخراج سنگ آهن تا نورد و تولید شمشهای فولادی بهعنوان محصول نهایی ادامه دارد و به نوعلی یکی از مراحل مهم در صنعت فولادسازی است. این فرآیند علاوه بر نیاز به تکنولوژی و نظارت های های پیشرفته، تاثیرات زیادی در اقتصاد و مسائل زیستمحیطی دارد. بهبود فرآیندهای تولید و استفاده از منابع جدید میتواند به کاهش هزینهها، افزایش کارایی و حفظ محیط زیست کمک کند. بهطور کلی، صنعت فولاد با توجه به نقش اساسیاش در ساخت زیرساختهای صنعتی و ساختمانی، همچنان بهعنوان یک بخش مهم در اقتصاد هر کشور از جمله ایران که در صنعت فولاد پیشرفت خوبی دارد محسوب میشود.
تولید شمش فولادی
تولید شمش فولادی شامل مراحل مختلفی از استخراج مواد اولیه تا تولید شمش نهایی است. این مراحل بهطور کلی شامل آمادهسازی مواد اولیه، ذوب سنگآهن، تبدیل چدن به فولاد، ریختهگری، و در نهایت تولید شمش فولادی میباشد.
فرآیند تولید شمش فولاد
تولید شمش فولادی یک فرآیند پیچیده و چندمرحلهای است که شامل استخراج مواد اولیه، ذوب و احیای سنگآهن، تبدیل چدن به فولاد، ریختهگری و در نهایت تولید شمش نهایی میشود. این شمشها بهعنوان مواد اولیه در تولید انواع مختلف محصولات فولادی کاربرد دارند و نقش حیاتی در تأمین نیازهای صنایع مختلف ایفا میکنند. توسعه فناوریهای نوین در هر یک از این مراحل میتواند باعث کاهش هزینهها، بهبود کیفیت، و افزایش بهرهوری در تولید شمش فولادی شود.
فرآیند تولید فولاد بهطور کلی شامل دو روش اصلی است که در تولید شمش فولادی تأثیر دارند:
تولید شمش در کوره بلند (Blast Furnace)
در روش کوره بلند، سنگآهن، کک، و سنگ آهک بهطور متناوب در کوره بلند قرار میگیرند. در این کوره، واکنشهای شیمیایی باعث کاهش اکسیدهای آهن به آهن مذاب میشوند. در نتیجه، چدن تولید میشود که نسبت به فولاد دارای مقدار زیادی کربن است. برای تبدیل چدن به فولاد، لازم است که میزان کربن آن کاهش یابد.
تولید شمش در کوره قوس الکتریکی (Electric Arc Furnace)
در روش کوره قوس الکتریکی، آهن قراضه (که معمولاً از ضایعات فولاد است) به همراه مواد اولیه دیگر وارد کوره میشود و با استفاده از قوس الکتریکی، آهن مذاب تولید میشود. این روش عمدتاً برای تولید فولادهای با آلیاژهای خاص یا فولادهای کمکربن بهکار میرود.
تولید شمش فولادی در کوره بلند
تولید شمش فولادی در کوره بلند یکی از روشهای رایج و قدیمی در صنعت فولاد است. این فرآیند با استفاده از سنگآهن، کک، و سنگ آهک به تولید چدن مذاب میپردازد که میتواند در فرآیندهای بعدی تبدیل به فولاد شود. با وجود مزایای بسیاری مانند ظرفیت تولید بالا و هزینههای کمتر در مقیاس بزرگ، این روش با چالشهایی مانند مصرف بالای انرژی و تولید آلودگیهای زیستمحیطی نیز همراه است.
مراحل تولید شمش فولادی در کوره بلند
مراحل فرآیند تولید شمش فولادی در کوره بلند عبارت اند از:
- بارگیری مواد اولیه
- دمیدن هوای داغ
- احیای سنگآهن و تولید چدن مذاب
- تشکیل سرباره
- ریختن چدن مذاب به کورههای فولادسازی
- کاهش کربن و تبدیل به فولاد
1- بارگیری مواد اولیه
برای شروع فرآیند، مواد اولیه شامل سنگآهن، کک، و سنگ آهک بهصورت لایهای در کوره بلند بارگیری میشوند. این مواد از طریق یک سیستم مخصوص به نام “بوشینگ” یا “خدمات بارگذاری” به داخل کوره منتقل میشوند. در این مرحله، سنگآهن بهصورت گلولههایی بهنام “Pellets” یا سنگآهن دانهبندی شده در میآید که برای افزایش سطح تماس با گازهای احیاکننده، به کوره فرستاده میشود.
2- دمیدن هوای داغ
در کوره بلند، هوای داغ به دمای حدود 1200 تا 1600 درجه سانتیگراد از طریق منافذ پایین کوره به درون کوره تزریق میشود. این هوا توسط کک میسوزد و به دمای بالا میرسد. هوای داغ همچنین با کک واکنش داده و دیاکسید کربن تولید میکند. در این مرحله، انرژی حرارتی زیادی برای فرآیندهای بعدی تأمین میشود.
3- احیای سنگآهن و تولید چدن مذاب
یکی از مراحل کلیدی در کوره بلند، احیای سنگآهن است. سنگآهن که معمولاً بهصورت اکسید آهن (Fe2O3 یا Fe3O4) وارد کوره میشود، تحت واکنش با کک که بهعنوان عامل احیاکننده عمل میکند، تبدیل به آهن (Fe) میشود. گاز کربن دیاکسید (CO2) حاصل از این واکنش، به همراه سایر گازهای تولیدی، از بالای کوره بلند خارج میشود. آهن حاصل از این واکنش بهصورت مذاب در بخش پایین کوره جمع میشود و بهعنوان چدن مذاب شناخته میشود.
4- تشکیل سرباره
در این مرحله، سنگ آهک وارد کوره بلند میشود و با ناخالصیهای موجود در سنگآهن مانند سیلیس (SiO2) واکنش داده و سرباره تولید میکند. سرباره یک ترکیب مذاب است که ناخالصیها را از آهن مذاب جدا میکند و بهعنوان یک محصول جانبی از کوره بلند خارج میشود. سرباره بهطور جداگانه از آهن مذاب جمعآوری میشود و معمولاً برای مصارف دیگر مانند راهسازی و ساخت سیمان مورد استفاده قرار میگیرد.
5- ریختن چدن مذاب به کورههای فولادسازی
چدن مذاب تولید شده در پایین کوره بلند بهطور مستقیم به کورههای فولادسازی منتقل میشود. این چدن ممکن است بهصورت یک محصول نیمهتمام یا بهعنوان ماده اولیه برای تبدیل به فولاد در فرآیندهای دیگر مانند کوره اکسیژنی (BOF) یا کوره قوس الکتریکی (EAF) استفاده شود.
6- کاهش کربن و تبدیل به فولاد
چدن مذاب تولید شده در کوره بلند دارای درصد بالایی کربن است و برای تبدیل به فولاد باید درصد کربن آن کاهش یابد. این فرآیند معمولاً در کورههای فولادسازی با استفاده از اکسیژن یا فرآیندهای دیگر انجام میشود تا کربن چدن کاهش یافته و فولاد با درصد کربن پایینتری تولید شود.
مراحل تولید شمش فولاد در کوره قوس الکتریکی
تولید شمش فولادی در کوره قوس الکتریکی یک فرآیند پیشرفته و کارآمد است که با استفاده از انرژی الکتریکی، آهن قراضه و مواد اولیه دیگر به فولاد مذاب تبدیل میشود. این فرآیند به دلیل کاهش مصرف انرژی، کاهش آلودگی محیطی، و امکان استفاده از مواد اولیه متنوع، مزایای بسیاری دارد. پس از تولید فولاد مذاب، ریختهگری شمش فولادی انجام میشود و این شمشها بهعنوان مواد اولیه در تولید انواع محصولات فولادی استفاده میشوند.
مراحل فرآیند تولید شمش فولادی در کوره قوس الکتریکی عبارت اند از:
- آمادهسازی مواد اولیه
- بارگذاری مواد اولیه به داخل کوره
- شروع فرآیند ذوب با استفاده از قوس الکتریکی
- فرآیند تصفیه و اصلاح ترکیب شیمیایی فولاد
- کنترل دمای فولاد مذاب
- پایان فرآیند ذوب و آمادهسازی برای ریختهگری
1- آمادهسازی مواد اولیه
برای شروع فرآیند تولید، ابتدا مواد اولیه باید آماده شوند. این مواد معمولاً شامل آهن قراضه بهعنوان ماده اصلی و بعضی افزودنیها برای بهبود کیفیت فولاد (مانند سنگآهن، فلزات آلیاژی و فریتها) هستند. مواد اولیه وارد کوره قوس الکتریکی میشوند و در این مرحله، ممکن است برای بهینهسازی مصرف انرژی و کیفیت، بهصورت لایهای چیده شوند.
2- بارگذاری مواد اولیه به داخل کوره
در مرحله بعد، مواد اولیه به داخل کوره قوس الکتریکی بارگذاری میشوند. این مواد بهطور معمول از طریق یک درب بالای کوره به داخل آن ریخته میشوند. در این مرحله، فولادسازان باید از مخلوط بهینه آهن قراضه و دیگر مواد اولیه اطمینان حاصل کنند تا کیفیت فولاد تولیدی مطابق با استانداردهای مورد نظر باشد.
3- شروع فرآیند ذوب با استفاده از قوس الکتریکی
با روشن شدن قوس الکتریکی، جریان برق از طریق الکترودهای کربنی که در قسمت بالای کوره قرار دارند، عبور میکند. قوس الکتریکی بهعنوان منبع اصلی گرما در کوره عمل میکند و دمایی بسیار بالا تولید میکند که به حدود ۳۰۰۰ درجه سانتیگراد میرسد. این حرارت بالا باعث ذوب آهن قراضه و سایر مواد اولیه میشود.
در این مرحله، گرمای تولید شده توسط قوس الکتریکی باعث ذوب سریع فلزات میشود و فولاد مذاب شروع به جمع شدن در بخش پایین کوره میکند.
4- فرآیند تصفیه و اصلاح ترکیب شیمیایی فولاد
در حین ذوب، آهن مذاب معمولاً شامل مقدار زیادی ناخالصی مانند کربن، فسفر، گوگرد و سیلیس است. برای تولید فولاد با کیفیت بالا، این ناخالصیها باید کاهش یابند. برای این منظور، در کوره قوس الکتریکی از اکسیژن و گازهای دیگری مانند آرگون برای تصفیه فولاد استفاده میشود.
- تزریق اکسیژن: با تزریق اکسیژن به داخل کوره، ناخالصیهایی مانند کربن و فسفر اکسید میشوند و به صورت گاز از کوره خارج میشوند. این فرآیند به کاهش کربن در فولاد و تولید فولاد با کربن پایین کمک میکند.
- افزودن مواد افزودنی: برای رسیدن به ترکیب شیمیایی مطلوب، برخی مواد آلیاژی مانند کروم، نیکل، منگنز، و وانادیوم به فولاد مذاب افزوده میشوند.
5- کنترل دمای فولاد مذاب
دمای فولاد مذاب باید در محدوده خاصی حفظ شود تا خواص مکانیکی و شیمیایی آن بهدرستی تنظیم شود. دمای فولاد مذاب معمولاً بین 1400 تا 1600 درجه سانتیگراد است و برای حفظ این دما، ممکن است نیاز به کنترل دقیق دمای کوره با استفاده از سیستمهای نظارتی پیشرفته باشد.
6- پایان فرآیند ذوب و آمادهسازی برای ریختهگری
پس از رسیدن فولاد مذاب به ترکیب شیمیایی مطلوب و دمای موردنظر، فرآیند ذوب در کوره قوس الکتریکی به پایان میرسد. در این مرحله، فولاد مذاب آماده است تا به مرحله بعدی فرآیند ریختهگری منتقل شود.
ریختهگری و تولید شمش فولادی
پس از ذوب شدن مواد اولیه و تولید فولاد مذاب در کوره قوس الکتریکی، فولاد مذاب به دستگاههای ریختهگری منتقل میشود. در این مرحله، فولاد مذاب بهصورت شمش فولادی یا بیلت ریختهگری میشود. برای این منظور، معمولاً از روشهای زیر استفاده میشود:
- ریختهگری پیوسته (Continuous Casting)
در این روش، فولاد مذاب بهطور پیوسته به داخل قالبهایی با مقاطع مشخص (مانند اسلب، بیلت، یا بلوم) ریخته میشود. در این فرآیند، فولاد مذاب بهسرعت از قالب عبور کرده و بهصورت شمش یا بیلت سرد میشود. این روش دارای مزایای زیادی از جمله کاهش هزینهها و افزایش بهرهوری است.
- ریختهگری گودالی (Ingots Casting)
در این روش، فولاد مذاب به داخل قالبهای مخصوصی ریخته میشود که معمولاً بهشکل بلوکهای بزرگ و سنگین هستند. این شمشها بهطور معمول برای فرآیندهای بعدی مانند نورد و شکلدهی به محصولات نهایی استفاده میشوند. این روش در حال حاضر در بسیاری از کارخانهها کمتر استفاده میشود، ولی هنوز در برخی از صنایع فولادی برای تولید فولادهای خاص کاربرد دارد.
جمع بندی
تولید شمش فولادی یکی از مهمترین مراحل در فرآیند تولید فولاد است که بهعنوان ماده اولیه برای تولید انواع محصولات فولادی مانند میلگرد، ورق، پروفیل، و لوله مورد استفاده قرار میگیرد. شمش فولادی معمولاً بهصورت بیلت (برای محصولات طویل) یا اسلب (برای ورقها) تولید میشود و بهعنوان ماده اولیه برای فرآیندهای بعدی مانند نورد و کشش مورد استفاده قرار میگیرد. این فرآیند میتواند با استفاده از دو روش اصلی کوره بلند (Blast Furnace) و کوره قوس الکتریکی (Electric Arc Furnace) انجام میشود که در مقاله فرآیند تولید شمش فولادی به طور کامل بررسی شده است. همچنین جهت تمایل میتوانید مقاله «عملکرد کوره ها در فولادسازی» را مطالعه بفرمایید.
پایان | وبلاگ قشم آهن (فولاد ابرکاوان قشم)
دیدگاه کاربران (0 دیدگاه)
اولین دیدگاه را شما ثبت کنید.